
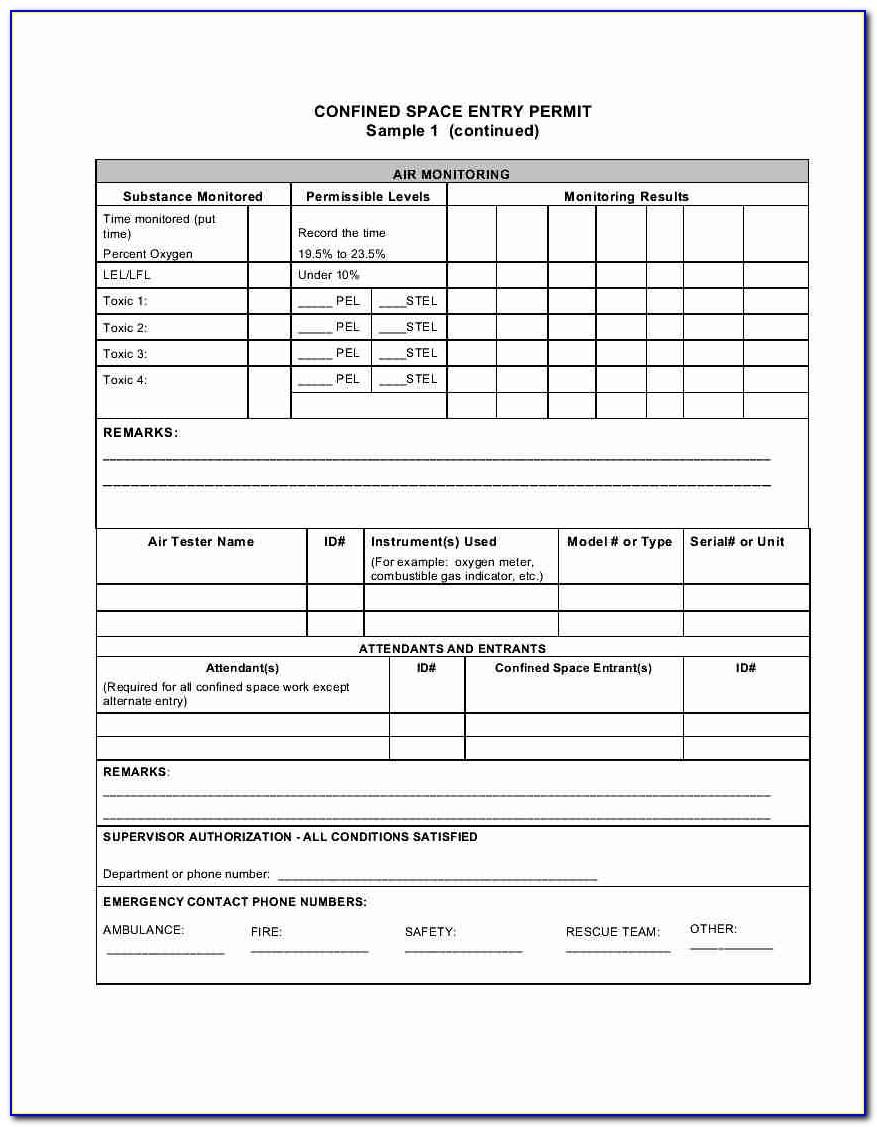
It can be difficult to determine when a machine must be locked out for servicing.

Each lockout tagout procedure should be well-documented and issues communicated clearly with all team members.Īn important regulation to remember: only those who performed the lockout/tagout procedure should sign off on bringing the forklift back into circulation once proper maintenance has been performed. Though it’s the responsibility of the facility manager to ensure proper steps are taken with lockout tagout procedures, it is also imperative for employees to learn and understand the process. Ensure isolation (lockout/tagout) of the forklift Who implements Lockout/Tagout procedures? Isolate forklift from any and all energy sourcesĥ. Shut forklift down using normal proceduresģ. Here are some basic guidelines for performing lockout and tagout procedures:Ģ. Though each facility may have a slightly different process, the steps are mostly the same. Steps to bring the powered lift trucks back into operation should also be clear and detailed. Having a detailed lockout/tagout program is one of the best ways to ensure that nobody gets injured and no machinery gets damaged. When developing a lockout/tagout program, the guidelines should be detailed and clear so that anyone reading them, even if they’ve never used the equipment before, can follow them correctly. The tagout tag provides detailed information about why the forklift is locked out. A lockout device uses a lock to hold an energy isolation device in a safe position and prevents the energy activation in the powered industrial trucks. In most lockout tagout procedures, a locked box is attached to the forklift, and a red and white warning tag is placed on the steering wheel.
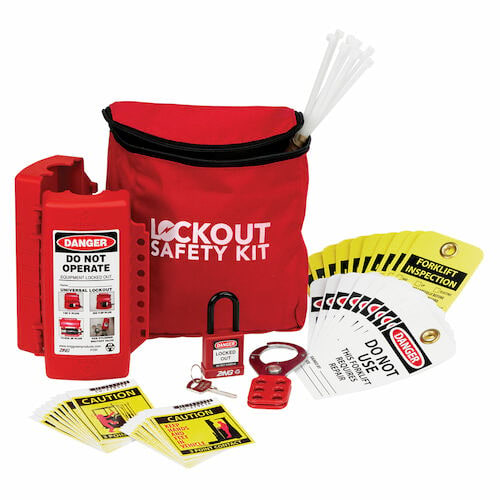
OSHA requires any facility with forklifts in operation to have a lockout tagout procedure in place. When done correctly, a lockout tagout procedure disables powered industrial trucks from releasing hazardous energy or starting unexpectedly during servicing or maintenance activities. Lockout tagout procedures help protect forklift operators and mechanics from unexpected electrical surges while maintenance is being performed. If damage has occurred, they must see to it that no further damage is caused. When a forklift goes down for any reason, the facility supervisor is tasked with ensuring the machine does not cause damage to the operator or product.
